Boiler Tube Plugs
Boiler Tube Plugs
When boiler tubes are suspected of leaking and the boiler’s efficiency has decreased, a vacuum test should be conducted on all tubes. The completion of these tests will confirm the condition of each tube. If feed water is observed leaking from a tube, then it indicates a compromised tube, necessitating the use of boiler tube plugs.
If feed water is seen running down the face of the tube sheet from the tube joint while the inside of the tube remains dry, the leak originates from the tube joint. In such cases, re-rolling the affected tube joint may be required. This type of leak becomes more apparent after a hydrostatic test. Re-rolling may seal the joint, but excessive re-rolling can exacerbate the issue by stretching the ligature between tubes, potentially causing leaks in adjacent tubes.
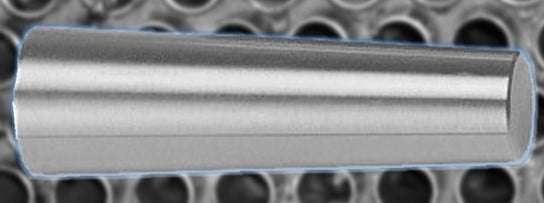
Boiler Tube Plug Sizes
1-1/2″ | 10-24 | 1.200″ | 1.495″ | 3″ |
1-1/2″ | 14-24 | 1.305″ | 1.600″ | |
1-3/4″ | 6-13 | |||
1-3/4″ | 14-22 | 1.575″ | 1.870″ | |
2″ | 6-13 | |||
2″ | 12-22 | 1.700″ | 1.995″ | |
2-1/4″ | 6-13 | 1.805″ | 2.100″ | |
2-1/2″ | 5-18 | 2.000″ | 2.375″ | |
2-3/4″ | 4-10 | 2.232″ | 2.500″ | |
3″ | 5-12 | 2.524″ | 2.834″ | 4″ |
3″ | 10-23 | 2.625″ | 3.000″ | |
3-1/4″ | 7-14 | 2.875″ | 3.125″ | |
3-1/4″ | 13-23 | 3.010″ | 3.250″ | |
3-1/2″ | 7-12 | 3.125″ | 3.375″ | |
3-1/2″ | 13-23 | 3.260″ | 3.500″ | |
3-3/4″ | 5-12 | 3.274″ | 3.567″ | |
3-3/4″ | 13-23 | 3.510″ | 3.750″ | |
4″ | 5-12 | 3.524″ | 3.817″ | |
4″ | 13-23 | 3.782″ | 4.000″ |
Plugs for any Type of Pressure vessel
We can supply you with any amount of boiler tube plug. We need the following information to quote you the best lead time if not in stock:
- Tube OD.
- Tube Wall Thickness.
- Operating Pressure of the Vessel.
- Material of the Tube.
- Number of Plugs required.
- How soon Required?
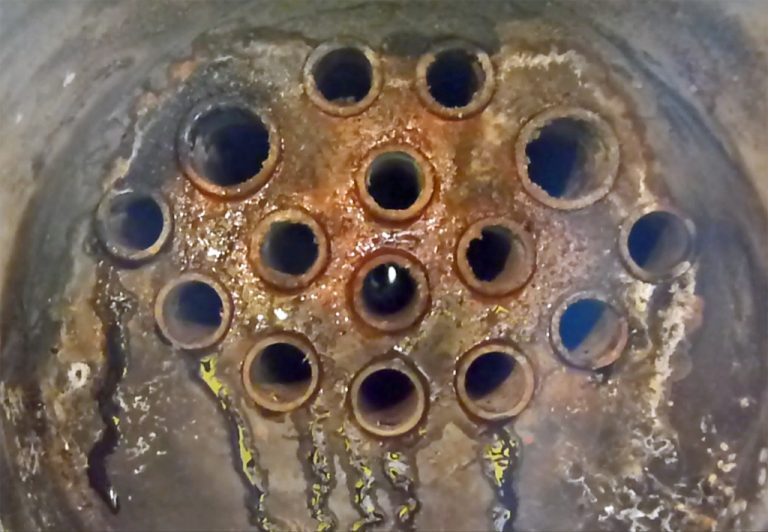
Piercing tubes before inserting Boiler Tube Plugs
Before welding, it is necessary for the technician to obtain the appropriate material certification for the plugs. This certification confirms the use of the correct plug type and allows for traceability should any issues arise. Heat lot numbers are available for SA-105 plugs, providing additional documentation that verifies the plugs’ integrity and quality.
Prior to inserting the plug into the defective tube, it is crucial to pierce the tube at both the top and bottom to prevent air from being trapped inside after plugging.
It is very important to allow water to flow through the tube to prevent internal pressurization.
Care must be taken to complete the welding according to the appropriate procedure. Neglecting proper procedures can result in damage to the tube sheet, which can lead to increased costs over time. Moreover, proper welding ensures that the plug is sealed as effectively as possible, which is particularly critical when the tube is more corroded. A well-executed weld can create a tight seal, preventing any leaks or dislodgement of the plug.
The optimal tool for this task is the One Revolution Internal Tube Cutter. As shown, this tool is manually operated using the socket and T-bar method. As the tool is rotated, the cutter extends from the tool and makes a complete cut through the tube wall. A short cut of approximately 20mm at both ends is sufficient. It is advisable to make the cuts at the top and bottom of the tube to ensure no air is trapped.
Carbon Steel Tube Plugs – Tube Plug Sizing Chart | ||||
Tube OD | Gauge | Dimension (Inches) | ||
“A” | “B” | “L” | ||
1/4″ | 18-24 | 0.141″ | 0.235″ | 1-1/4″ |
3/8″ | 12-24 | |||
3/8″ | 15-24 | 0.213″ | 0.371″ | 1-3/4″ |
1/2″ | 13-15 | |||
1/2″ | 15-24 | 0.337″ | 0.495″ | |
5/8″ | 12-14 | |||
5/8″ | 14-24 | 0.449″ | 0.625″ | |
3/4″ | 10-14 | |||
3/4″ | 14-24 | 0.564″ | 0.750″ | |
7/8″ | 10-13 | |||
1″ | 8-9 | |||
7/8″ | 15-24 | 0.706″ | 0.875″ | |
1″ | 10-15 | |||
1″ | 13-18 | 0.776″ | 0.934″ | |
1″ | 18-24 | 0.892″ | 1.050″ | |
1-1/8″ | 13-17 | |||
1-1/8″ | 15-24 | 0.949″ | 1.125″ | 2″ |
1-1/4″ | 10-14 | |||
1-1/4″ | 13-19 | 1.010″ | 1.186″ | |
1-1/4″ | 19-24 | 1.147″ | 1.323″ |